Durante todo el año recibimos muchos mail,
pidiéndonos información para realizar trabajos sobre autómatas. Así que ahora es
el momento para recordaros que necesitamos de vuestra colaboración enviándonos
los que ya habéis presentado.
| |
Why ControlNet?
From proprietary to public standard, the proliferation of industrial networks
offers users various benefits, but unfortunately from different networks. Couple
this with the flattening of architectures and demands for higher performance,
and you can see there was a need for an automation and control network that
combined the benefits of several networks onto one link for increased system
performance. Also needed was a control network to reliably predict when data
will be delivered and ensure transmission times are constant and unaffected by
devices connecting to, or leaving, the network.
These realities drove the development of ControlNet ... a real-time, control-layer
network providing high-speed transport of both time-critical I/O data and
messaging data, including upload/download of programming and configuration data
and peer-to-peer messaging, on a single physical link. ControlNet's high-speed
(5 Mbits/sec) and configurable data transmission capabilities significantly
enhance I/O performance and peer-to-peer communications.
Taking full advantage of the Producer/Consumer model, ControlNet allows
multiple controllers to control I/O on the same wire. This provides significant
advantage over other networks, which allow only one master controller on the
wire. ControlNet also allows multicast of both inputs and peer-to-peer data,
thus reducing traffic on the wire and increasing system performance.
ControlNet is highly deterministic and repeatable -- critical requirements
for ensuring dependable, synchronized and coordinated real-time performance.
Determinism is the ability to reliably predict when data will be delivered, and
repeatability ensures that transmit times are constant and unaffected by devices
connecting to, or leaving, the network. These features are further enhanced with
user selectable I/O and controller interlocking update times to match
application requirements.
ControlNet provides
 | Bandwidth for I/O, real-time interlocking, peer-to-peer messaging and
programming
all on the same link
 | Deterministic, repeatable performance for both discrete and process
applications
 | Multiple controllers controlling I/O on the same link
 | All data maybe multicast, including inputs, outputs, and peer-to-peer
 | Media redundancy and intrinsically safe options
 | Simple installation requiring no special tools to install or tune the
network
 | Network access from any node
 | Flexibility in topology (bus, tree, star) and media types (coax, fiber,
other) |
| | | | | | |
How it works
Network access is controlled by a time-slice algorithm called Concurrent Time
Domain Multiple Access (CTDMA), which regulates a node's opportunity to transmit
in each network interval. You select the length of the network interval by
selecting a network update time (NUT). For example, 2ms, 20ms, 50ms, etc. The
fastest NUT you can specify is 2 ms.
Information that is time-critical is sent during the scheduled portion of the
network interval. Information that can be delivered without time constraints (such
as configuration data) is sent during the unscheduled part of the network
interval. Time-critical control data is delivered every NUT in a deterministic,
repeatable fashion. Non-time-critical data is delivered as unscheduled time
permits.
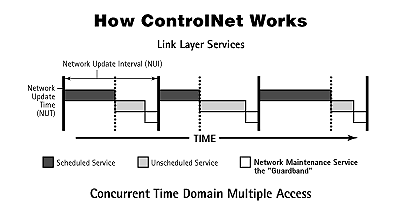
Where does ControlNet fit?
Plant-floor
architectures are flattening into three layers:
 | Information layer for plant-wide data collection and program
maintenance
Example: Ethernet
 | Automation and Control Layer for real-time I/O control, interlocking,
and messaging
Example: ControlNet
 | Device Layer for cost-effective integration of low-end devices
Example: DeviceNet, Foundation Fieldbus |
| |
ControlNet meets the demands of real-time, high speed applications at the
Automation and Control Layer for integration of complex control systems such as
coordinated drive systems, weld control, motion control, vision systems, complex
batch control systems, process control systems with large data requirements, and
systems with multiple controllers and human-machine interfaces. ControlNet is
ideal for systems with multiple PC-based Controllers, PLC-to-PLC and PLC-to-DCS
communication.
ControlNet Architecture Capabilities
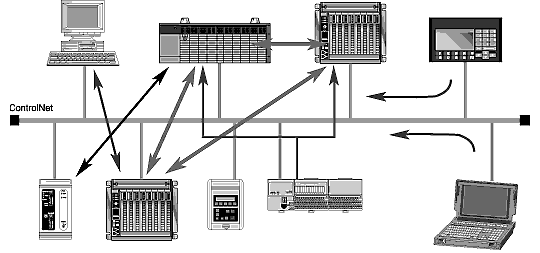
ControlNet allows multiple controllers on a single link to
share inputs while controlling their own outputs. Controllers can also talk to
each other in any possible combination with both scheduled interlocking data and
unscheduled messaging data.
Producer/Consumer Communication
The Basis of ControlNet's Advanced Features
The capabilities of traditional networks cannot satisfy the ever-increasing
demands for higher productivity and greater system performance, while providing
for repeatable and predictable communication between devices. Higher baud rates
and greater protocol efficiency, alone, are not enough to meet the challenge. A
state-of-the-art approach is needed for the basic technology of how a network
manages communications with connected devices (nodes).
ControlNet is based on an innovative solution in open network technology: the
Producer/Consumer model. Unlike its predecessors, the Producer/Consumer model
permits all nodes on the network to simultaneously access the same data from a
single source. Ultimately, this model provides:
 | Greater system performance for higher productivity
 | Increased efficiency because data needs to be produced only once,
regardless of the number of consumers
 | Precise synchronization because data arrives at each node at the same time |
| |
The "New" Communication Model
Older network communication models use "Source/Destination" or
point-to-point communication models. Source/Destination wastes bandwidth as like
data must be sent multiple times when only the destination is different. Also,
synchronization
between nodes is very difficult as data arrives at a different time to each node.
With Producer/Consumer, the data has a unique identifier. Using this model,
multiple nodes can consume the same data at the same time from a single producer,
resulting in more efficient use of bandwidth. Also, nodes can be easily
synchronized.
Example: Communicate the current time-of-day to a room of
twenty (20) people.
Source/Destination Model
One person ("source") tells each person ("destinations")
in the room, one at a time, the current time-of-day (data).
INEFFICIENCIES
 | Excess Data Transmission - some people may choose to listen; others may
choose to ignore.
 | Data Inaccuracies - Time will pass during multiple transmissions,
compromising data accuracy.
 | Determinism Fluctuations - The length of time to deliver data is dependent
on the number of people in the room. |
| |
Producer/Consumer Model
One person ("Producer") tells ALL people ("Consumers") in
the room AT THE SAME TIME the current time-of-day (data).
HIGHLY EFFICIENT
 | Economy of Data Transmission - No wasted effort delivering data to those
who do not care.
 | Accurate Data - No adjustments to data needed since everyone received the
data at the same time.
 | Deterministic - Length of time to deliver data is independent of the
number of people in the room. |
| |
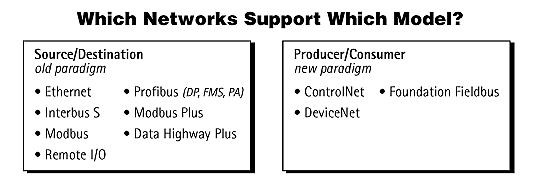
http://www.controlnet.org
ControlNet is a Trademark of ControlNet International, Ltd.
DeviceNet is a Trademark of the Open DeviceNet Vendor Association, Inc.
| | |